Context and challenges in the design of microsurgical instruments.
The design of microsurgical and endoscopic instruments is currently confronted with a limit to the characteristics of the materials and implementation solutions proposed.
The trend in user demand is towards greater quality and precision and that of health service funders towards ever more affordable access to care.
The demands for innovation in operating techniques are to facilitate the surgeon’s work by offering more precision while reducing fatigue by improving the ergonomics and performance of instruments. In the meantime, there is a need to further miniaturise the instrument to reduce its invasiveness. They must also respond to the demand for cost reduction by proposing economical solutions for the development of instruments, through new manufacturing processes that reduce manufacturing ranges, better durability and reduced maintenance.
The new requirements of both users and manufacturers of microsurgical instruments are leading to changes in their design, very often by directing innovation towards geometric optimisation, particularly to improve ergonomics and functionality. Improvements in the metals used in the medical field are rarer and 316L stainless steel and Titanium (TA6V) still remain the references.
At the same time, manufacturing resources such as the latest generation of numerically controlled machines or metal additive manufacturing make it possible to produce medical devices such as instruments, implants and components of medical devices. However, the production of miniature components for minimally invasive instruments remains a challenge due to the high cost of achieving the dimensions, tolerances and surface finishes required for their new designs.
The proposed approach is the production of instruments in Amorphous Metal Alloy, associated with manufacturing processes of the “thermo-moulding” type.
It is a technological breakthrough combining innovative materials with unequalled mechanical and physical characteristics and a final shaping that provides greater precision, new geometries, a reduction in manufacturing stages and a reduction in production costs.
The combination of material and process is the crucial issue in order to successfully meet the combination of requirements mentioned above.
A design example with an innovative microsurgery clamp made of Vulkalloy®:
The technologies proposed by Vulkam respond in a differentiated way to the new challenges of the micromechanical industries at two levels.
- The first level is associated with the specificity of amorphous metal alloys which present exceptional mechanical, physical and chemical characteristics.
- The second level is related to the unique processing methods that allow the production of unique, high precision miniature components. The design of an innovative microsurgery forceps made of Vulkalloys® Amorphous Metal Alloy combines these two significant advantages over current solutions :
Vulkalloy® Zr-Med, an innovative alloy for miniaturization : it has unmatched mechanical properties.
As shown in the table below, Vulkalloy® Zr-Med far exceeds other alloys traditionally used in the medical field with an elastic stress twice as high as TA6V which is the reference in the field. In addition, the exceptional characteristics of Vulkalloy® Zr-Med allow a specific strength of up to 250 kN.m.kg-1.
These characteristics result in a much higher strength, a very good flexibility while offering the possibility to significantly reduce the weight and dimensions of the instruments. These characteristics allow for increased mechanical strength, durability, and reduced maintenance with a consequent saving on the cost of managing the instrument fleet. These unequalled mechanical characteristics allow a miniaturized design of the instrument to reduce its invasiveness. Finally, Vulkalloy® Zr-Med is biocompatible. Cytotoxicity and metal release tests according to Iso 10993 standards have been successfully performed.

A competitive production process that guarantees the amorphous structure and associated properties
The use of Vulkalloy® Zr-Med by an innovative and unique thermo-moulding process developed by Vulkam offers a real technological and economical breakthrough for the production of miniature components constituting microsurgical instruments. Their design in Vulkalloy® metal alloy associated with the thermo-moulding process offers a unique differentiation in several ways:
- Once the alloy has been produced, its injection by thermo-moulding allows the final shaping of the clamp tips, for example, in a single step to the required dimensions, tolerances, surface finishes and roughness. Current processes for making miniature components often include costly technologies with a succession of more important steps such as sheet metal working, cutting, bending, machining, shaping, grinding, reworking, polishing, often manually, as well as heat or surface treatments. This simplifies the manufacturing process, making it fast and economical, particularly by limiting the number of time-consuming and costly manual steps, depending on the type of component and series concerned.
- Access to Vulkalloys® Amorphous Metal Alloy thermo-moulding technology allows the manufacture of forceps tips or instrument components that are difficult to produce by conventional means, in particular because of the ability to shape by injection a very wide range of geometries related to the function (gripping, biopsy, dissection, extraction, applicator. .) and surface conditions (serrations, striations,…) by obtaining dimensional accuracies of up to 1µm and roughnesses of up to Ra = 0.2 µm depending on the type of mould used (metal, silicon…).
- It is an industrial process perfectly suited to the production of single-use instruments as well as reusable medium and large series, once the tooling has been designed and produced, with high reproducibility and repeatability to ensure the quality of the parts.
- Vulkam’s technology saves metal resources, which have a strong impact on the environment : stronger, more durable and miniaturizable parts that contribute to the design of mechanical sub-assemblies that last longer and save the energy of their implementation. In addition, the production technology limits pollution and allows for almost total recycling of the material with a “zero waste” objective. In the long term, the environmental impact of Vulkam’s activity contributes, on its own scale, to the saving of strategic resources for the industry.
- Vulkam’s process also fits perfectly with any innovative and ambitious industrial strategy of Vulkam’s partner companies with a “proximity sourcing” policy chosen to keep control of the development of high added value solutions while preserving intellectual property, know-how and competitive differentiation on the international market of miniature components
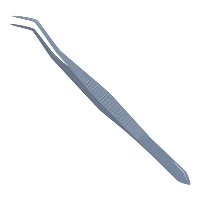
The design of a microsurgical instrument in Vulkalloy® Zr-Med, thanks to a unique technology of elaboration of the material with unequalled characteristics associated with a unique thermo-moulding process, opens up a field of incomparable technical, economic and strategic opportunities to any industrialist of the Medical Devices sector wishing to differentiate itself on the market.
Vulkam, an innovative metallurgy company serving the medical and dental industry
Vulkam is an SME specialized in Amorphous Metal Alloys which has developed a range of new metals with incomparable properties, the Vulkalloys®. Its technology is based on changing the atomic organisation of metals to fundamentally change the mechanical properties of the parts produced. Vulkalloys® parts are produced by a unique proprietary process. It is specifically developed for these materials and is totally adapted to miniature components (a few tenths of a mm to a few cm). Its two patented steps allow the production of parts with fewer manufacturing steps, variable shapes, precision, excellent surface finish and optimised geometries.
For more information, visit our Web site : www.vulkam.com