Cas d’usage : Comparaison entre une lunette de montre produite en Vulkalloy® Zr-Inox et une lunette fabriquée en Alliage de Titane TA6V
Limiter les pertes de matière et l’impact environnemental
Vulkam a développé une technologie plateforme permettant de mettre en œuvre un procédé de production prenant en compte de manière centrale et forte les enjeux environnementaux :
- Pour réduire la consommation en métaux et ressources primaires : Des procédés « near net shape » optimisés au plus proche de la forme finale (versus « standard shape »)
- Pour réduire la consommation énergétique des procédés industriels : Des volumes inférieurs, une boucle quasi infinie et noble de réutilisation des carottes d’injection en production.
Le Vulkalloy® Zr-Inox
Le Vulkalloy® Zr-Inox a été développé pour l’habillage horloger, l’industrie du Luxe, la production de pièces d’aspect telles que boites, lunettes, maillons, bouclerie et la bijouterie.
Les avantages de ce matériau (résistance aux chocs, aux rayures, grande polissabilité, tenue à la corrosion et grande stabilité dans le temps) couplés au procédé de fabrication « near net shape » en font une solution « matériau » innovante et particulièrement économe en volume de matière nécessaire, en consommation d’énergie et en émissions de CO2 par rapport à une solution en Alliage de Titane.
Les avantages de ce matériau (résistance aux chocs, aux rayures, grande polissabilité, tenue à la corrosion et grande stabilité dans le temps) couplés au procédé de fabrication « near net shape » en font une solution « matériau » innovante et particulièrement économe en volume de matière nécessaire, en consommation d’énergie et en émissions de CO2 par rapport à une solution en Alliage de Titane.
Comparaison chiffrée : Le cas de la lunette horlogère
Le cas d’Usage est présenté ci-dessous : Notre Client souhaite réaliser une lunette de montre en Vulkalloy® Zr-Inox, sélectionné pour son aspect, sa très grande durabilité et son bilan en termes de consommation de ressources.
Les dimensions attendues sont les suivantes : 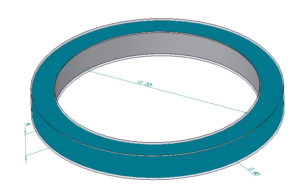
Les dimensions attendues sont les suivantes :
- Diamètre extérieur : 40 mm
- Diamètre Intérieur 33 mm
- Epaisseur : 4 mm
- Volume net de la pièce : 1600 mm3
Pour ce faire, l’équipe technique de Vulkam conçoit une ébauche « near net shape » (dimensions optimisées au plus proche de la pièce finale) de 1875mm3, intégrant une surépaisseur de 0.3mm.
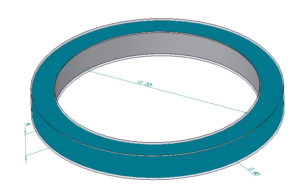
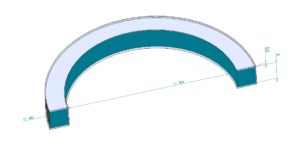
Après moulage, le volume qui devra être usiné pour obtenir la lunette de montre dans sa dimension finale est de 275mm3 : Ceci représente une perte de moins de 15% de matière seulement.
De plus, le procédé Vulkam permet une maîtrise de la qualité matière tout au long de la chaîne de production, ce qui rend possible le recyclage des « carottes d’injection », directement réutilisées dans la boucle de fabrication et réintégrées en début de chaîne de production.
De plus, le procédé Vulkam permet une maîtrise de la qualité matière tout au long de la chaîne de production, ce qui rend possible le recyclage des « carottes d’injection », directement réutilisées dans la boucle de fabrication et réintégrées en début de chaîne de production.
Si notre Client s’était tourné vers un mode de production industriel d’usinage traditionnel, l’équipe technique aurait conçu une ébauche à partir d’une barre pleine d’alliage de Titane TA6V standard, de diamètre 45mm, d’un volume brut de 9550mm3 nécessitant une surépaisseur d’usinage de 2mm.
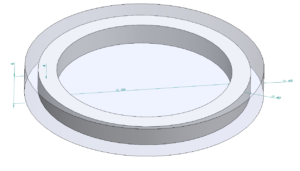
Pour obtenir la lunette de montre dans sa forme finale, le volume usiné (perdu) aurait été de 7950mm3, soit une perte de matière de 83%, soit 6 fois plus que via le procédé Vulkam.
De plus, ces 7950mm3 de copeaux en sortie de chaîne de fabrication sont ensuite jetés ou refondus pour des applications « rebuts » bien moins nobles, au cours d’un second cycle énergétique tout aussi énergivore et peu efficient.
Pour ce premier point, les pertes et le gaspillage de ressources en matières premières « métaux » sont donc conséquents puisque divisés par 6 grâce au procédé Vulkam, intégrant le moulage « near net shape » couplé au recyclage efficient des carottes.
En ce qui concerne le second point et les gains énergétiques de production, ceux-ci intègrent et comparent :
- L’extraction, la fonderie, le laminage et l’usinage pour le Titane
- L’extraction, l’élaboration de la matière et le thermomoulage sur un même site, puis l’usinage pour le cas du Vulkalloy® Zr Inox.
Les gains ainsi obtenus d’un point de vue énergétique sont conséquents et de l’ordre de 30% :
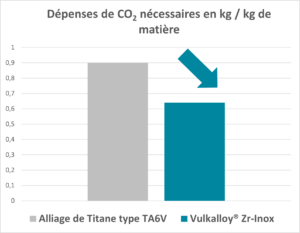
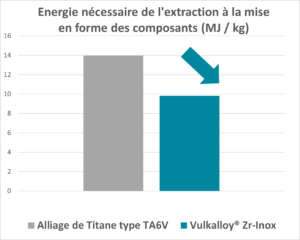
En effet, au cours des procédés industriels classiques, des barres ou plaques de dimensions standards et non optimisées sont utilisées, la matière est très difficilement et très peu recyclée, majoritairement mise au rebut sans possibilité de « boucle de réutilisation ».
En comparaison, le procédé global « Near net shape + recyclage des carottes d’injection » représente une voie de fabrication optimisée de pièces au plus proche de la forme finale, où l’énergie nécessaire à produire la préforme est valorisée soit dans le produit, soit dans le recyclage.
Le procédé « near net shape » est particulièrement efficient, économique et économe en énergies de production, permettant ainsi de diviser les pertes et le gaspillage de ressources par 6.
Si vous souhaitez en savoir plus et intégrer ce procédé pour vos pièces d’habillage, n’hésitez pas à contacter nos équipes techniques.
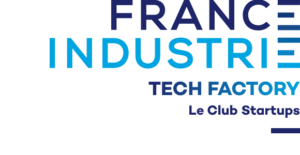